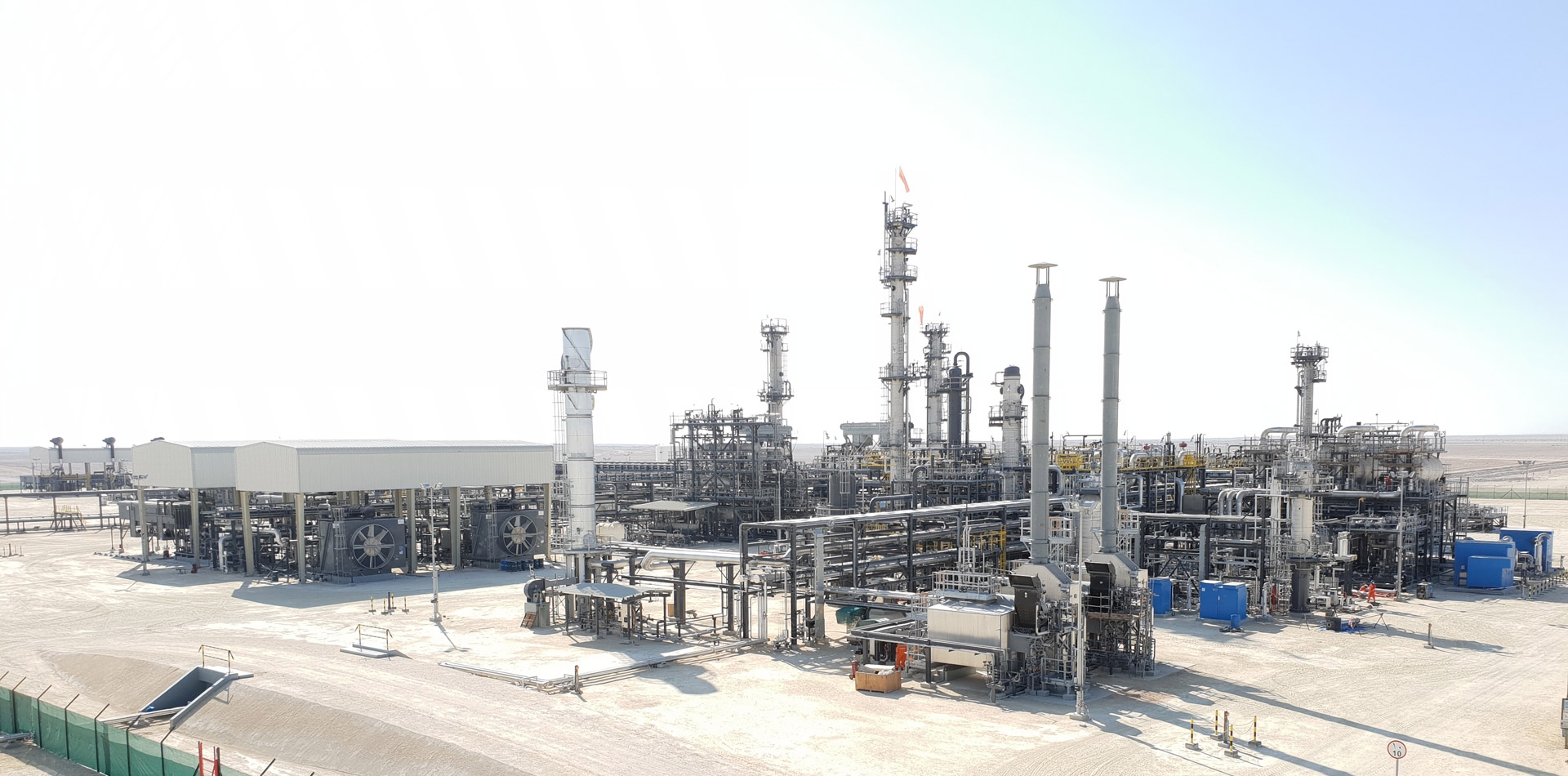
Equipment
Gas Processing
Tailored Solutions from Wellhead to Pipeline
Enerflex offers modular gas processing solutions across every major oil and gas basin. We use our decades of local expertise to provide customized solutions that meet your specific operational needs.
The Enerflex Edge
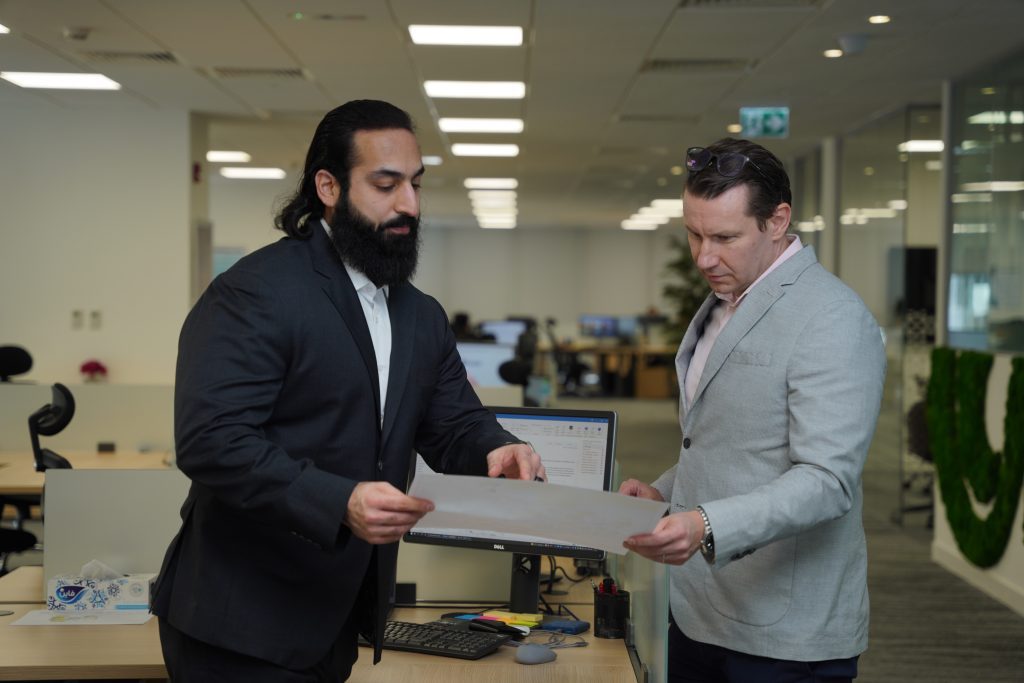
We Think Relationships First
We develop strong partnerships with our clients. By understanding the nuances of their challenges, we deliver top-tier customized gas processing solutions, ensuring reliable, efficient operations.
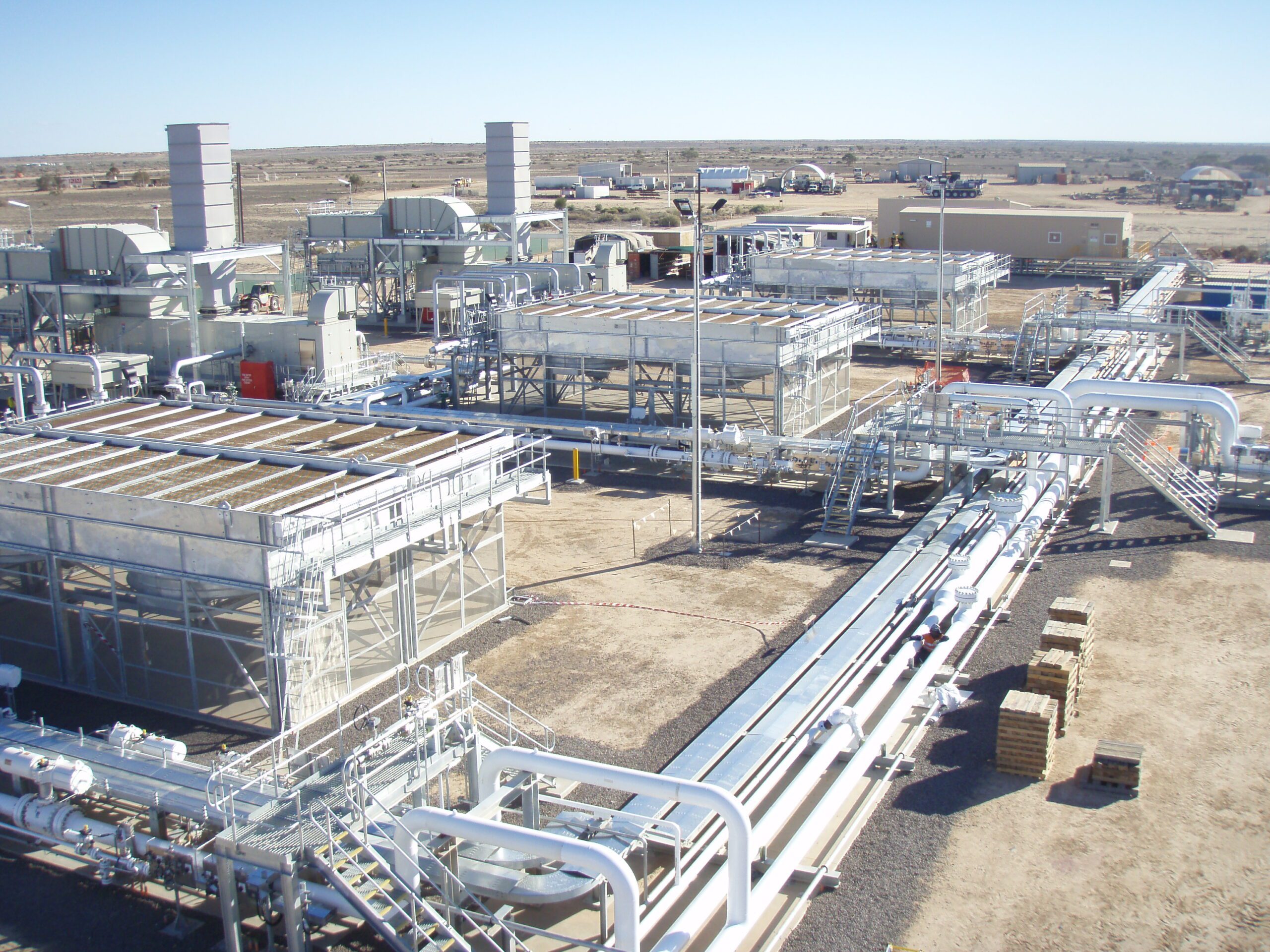
Comprehensive FEED Studies
We provide front-end engineering design, helping our client partners plan their projects with precision before the full project commitment.
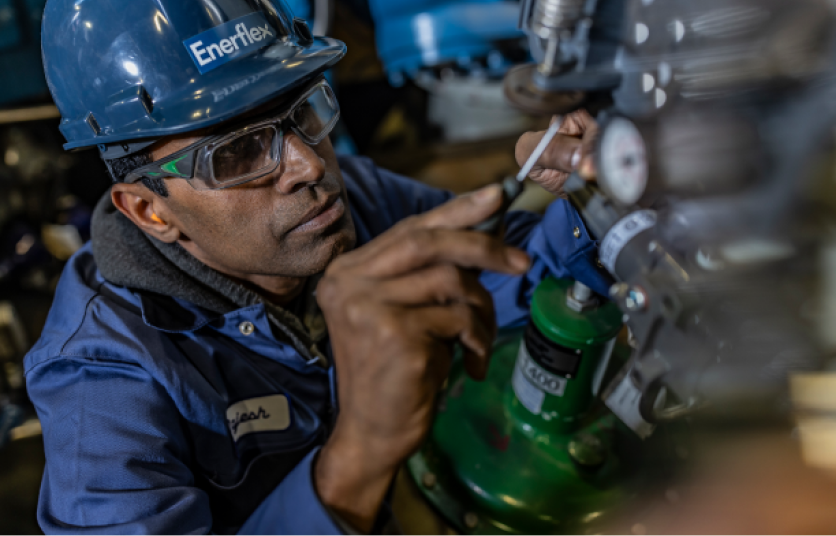
Proven Track Record and Technical Expertise
With over 45 years of experience and hundreds of successful projects, we’ve earned a reputation as a leading provider in the industry. Our technical expertise translates to design, cost and time efficiencies, ensuring superior solutions.
500+
Gas processing facilities installed
26
Gas processing facilities Enerflex operates on behalf of client partners
100+
Cryo projects installed globally
710K
Manufacturing capacity
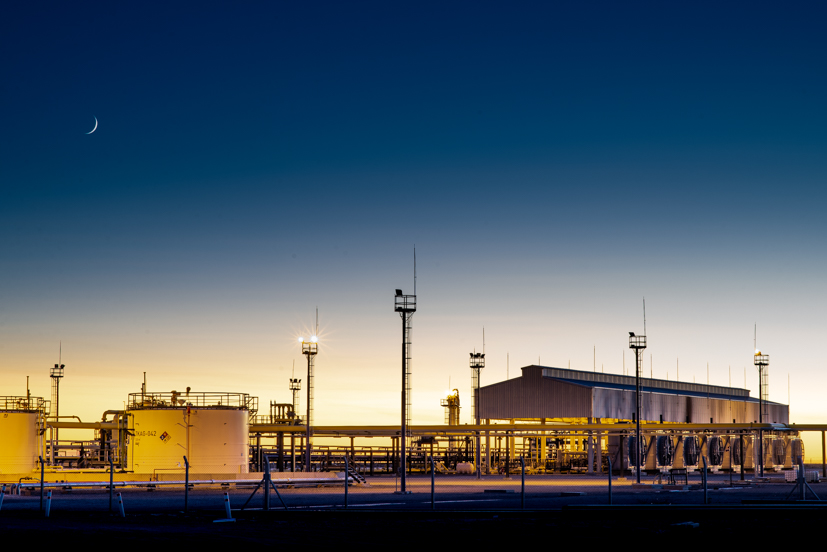
Custom Gas Processing Solutions
Enerflex delivers custom gas processing systems that address the unique needs of each project, maximizing operational flexibility while meeting stringent industry standards. With operator training and ongoing after-market support, these solutions are designed for long-term success in any environment.
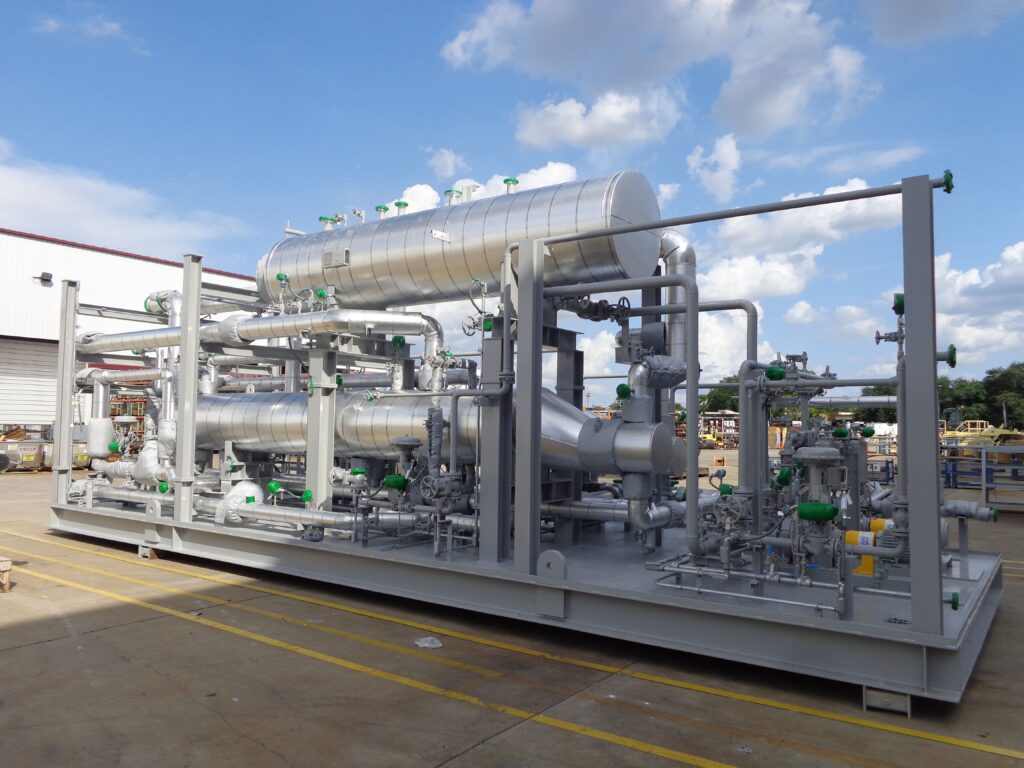
Pre-Engineered Gas Processing Solutions
Our pre-engineered gas processing solutions offer fast deployment and reliable performance, reducing on-site installation time and costs. All modules come equipped with LC or DCS-based automatic sequencing controllers, ensuring seamless operation, with scalable options for future upgrades.
Complete Gas Treating and Processing Capabilities
Pre-Treating
- Inlet Separation / Filtration
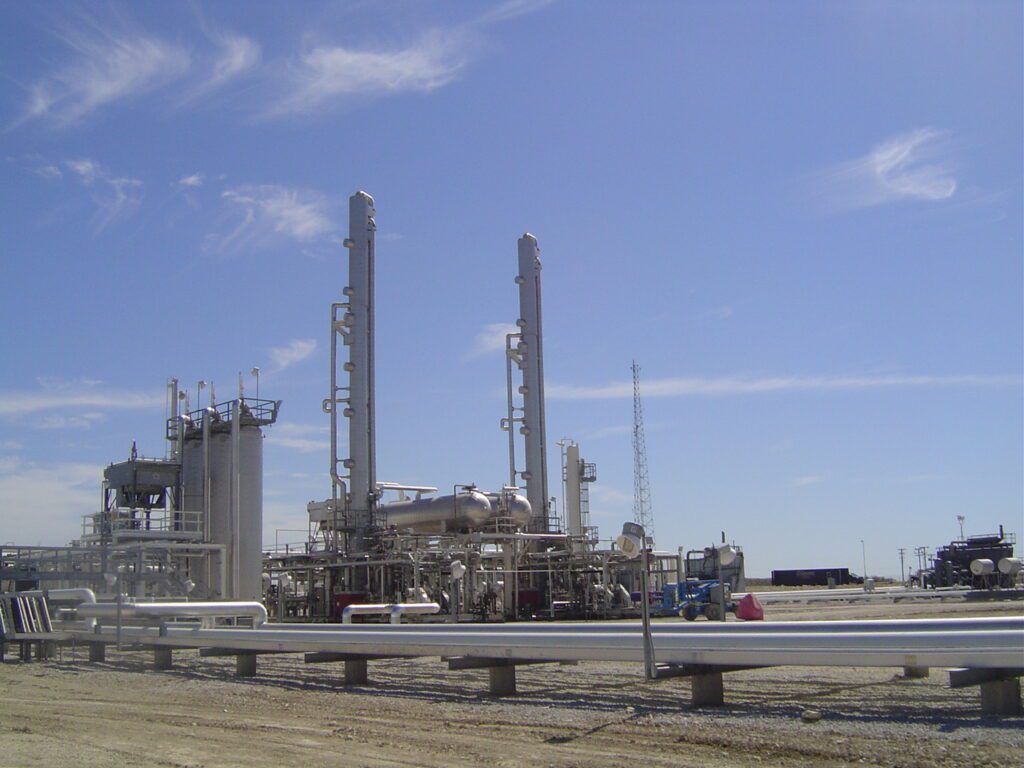
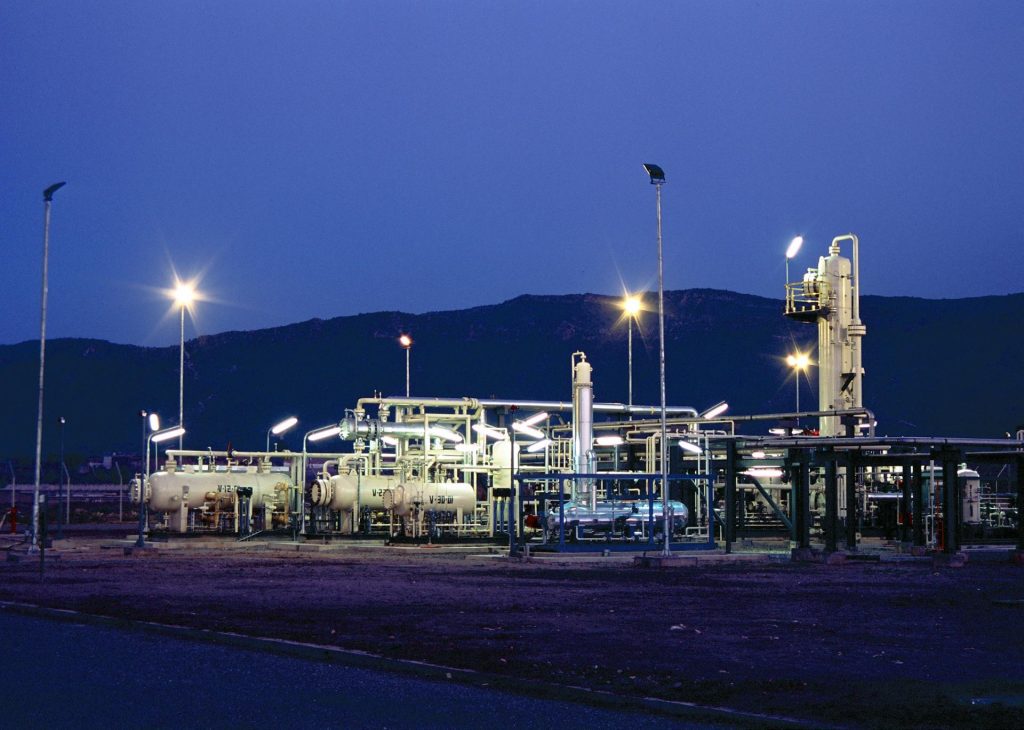
Hydrocarbon Treating
- Dehydration – TEG, Molecular Sieve, Silical Gel
- Sweetening – Amine, Hybrid Solvent, Solid Scavenger
Hydrocarbon Liquid Handling
- Cryogenic / Deep Cut
- Stabilization
- Flare Gas
- LPG Extraction
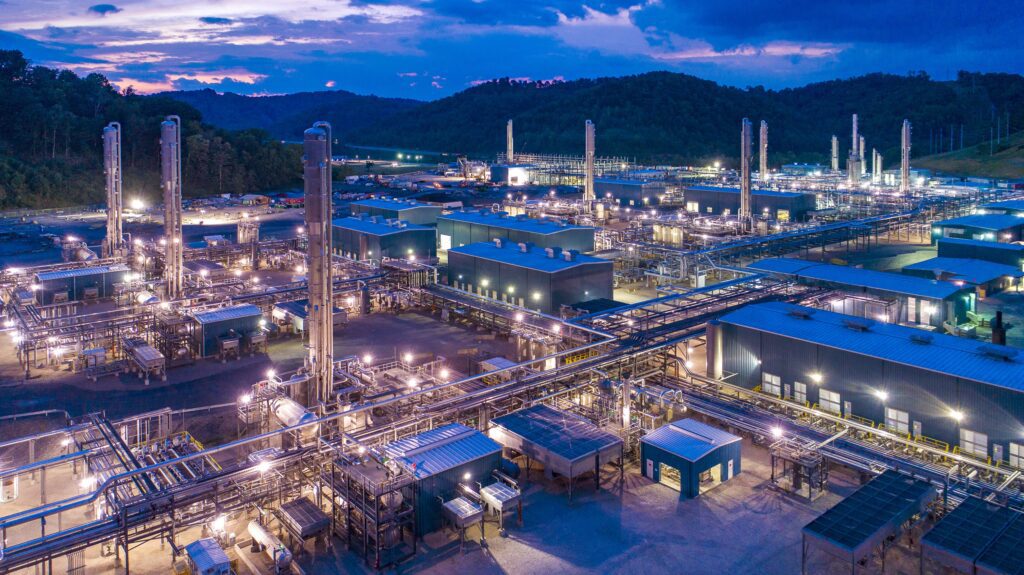
Case Study
Canada – Cabin Creek Gas Plant Processing Facility
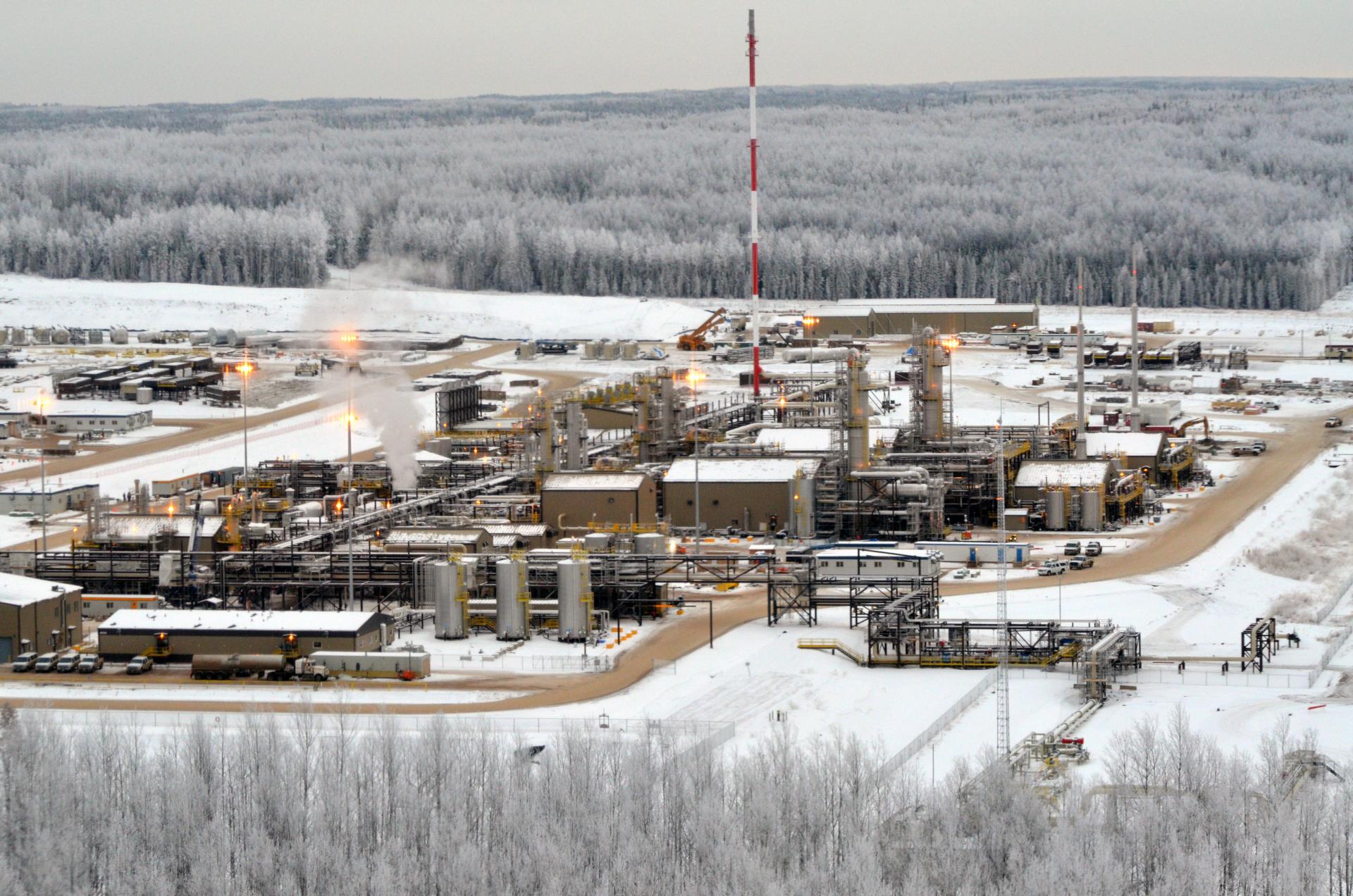
Challenge:
Enerflex was commissioned to provide 17,000 HP of compression, modular amine units for H₂S and CO₂ removal, and dehydrators. The project required 58,000 engineering hours, 350,000 shop hours, and 600 trailer loads, including 70 assembled process modules.
Solution:
Enerflex supplied four amine trains, each processing 200 MMSCFD with a combined circulation of 8,400 GPM. Modularized design minimized field installation time.
Outcome:
The facility became the largest sour gas processing plant in the region, handling 800 MMSCFD of raw gas. Enerflex’s modularized approach ensured a smooth, timely installation and efficient operation.
Case Study
104 MMSCFD Gas Processing and Treating Facilities
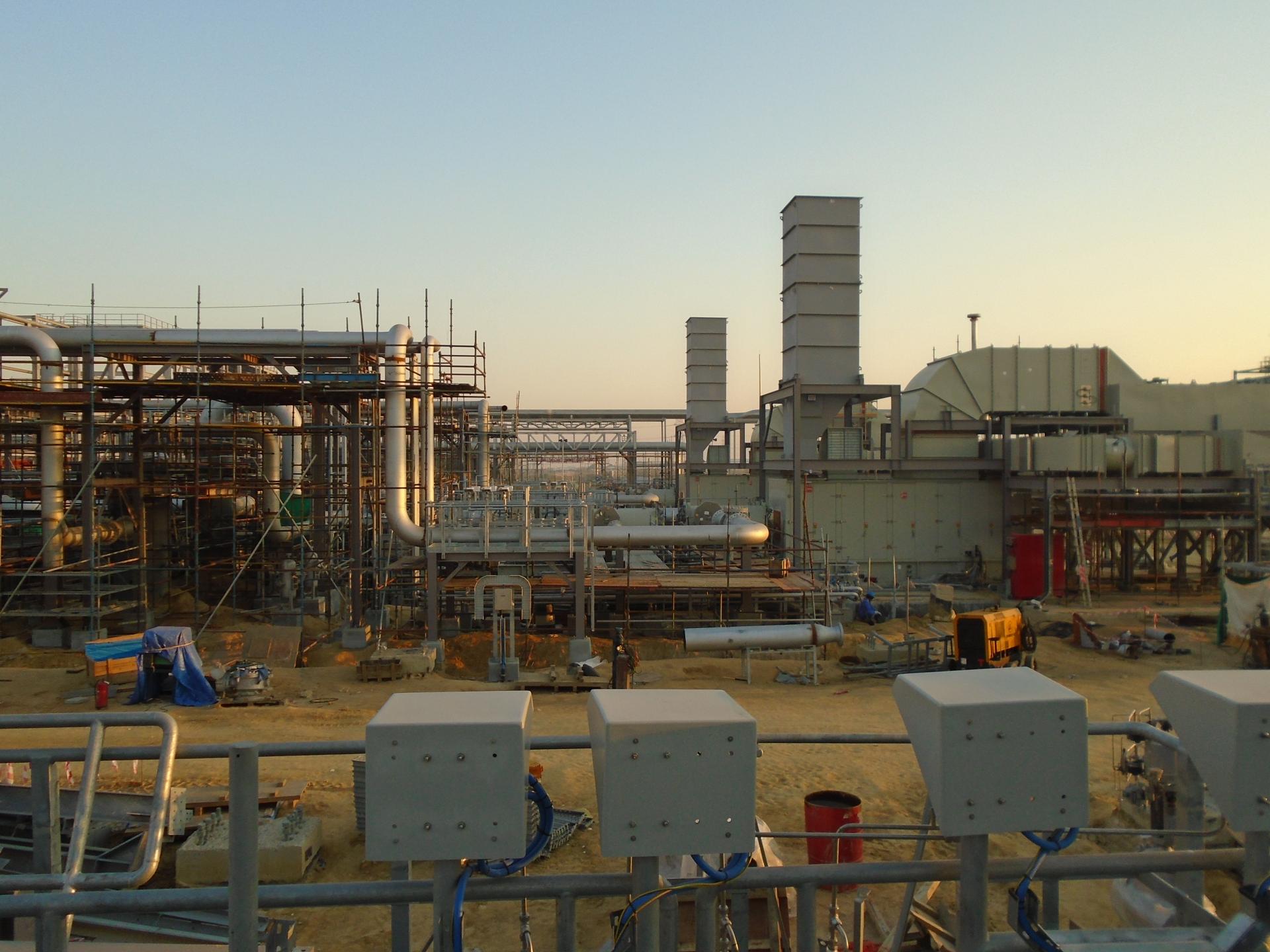
Challenge:
Enerflex was contracted to design and deliver two large natural gas compression and process and treating facilities in Kuwait. The project required collaboration across teams from Abu Dhabi, Houston, and Calgary to engineer, install, and commission gas compressors, propane refrigeration, amine packages, TEG units and other equipment to cover the full project scope.
Solution:
Enerflex provided modularized solutions for two 104 MMSCFD facilities, integrating advanced gas processing equipment. The collaboration among global teams ensured efficient delivery and installation.
Outcome:
Both facilities were completed on-time and within budget. The success of the project highlighted our global reach, engineering expertise and prowess in executing large-scale projects.
Comprehensive Infrastructure for Gas Processing
Our infrastructure capabilities for gas processing include full-service Build-Own-Operate-Maintain (BOOM) solutions. We handle design through operations to optimize performance, reduce costs, minimize risks, and accelerate gas-to-market timelines.
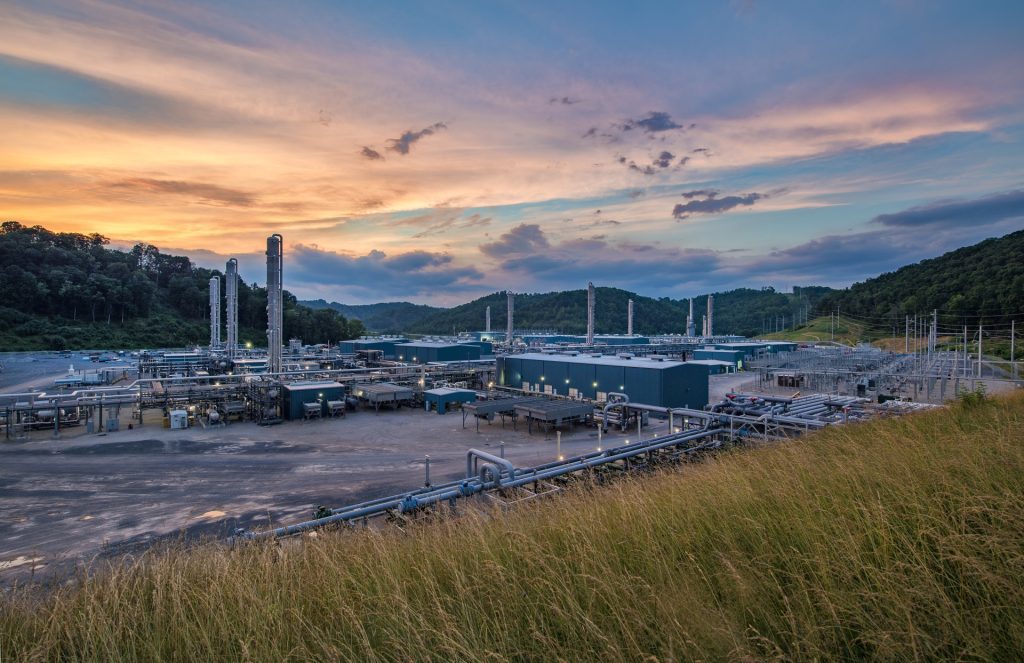
Certifications
Our gas processing equipment is compliant with all major codes.
- ASME
- AISC
- NEC
- ISA